Understanding the Dynamics of Plastic Injection Molding Manufacturers
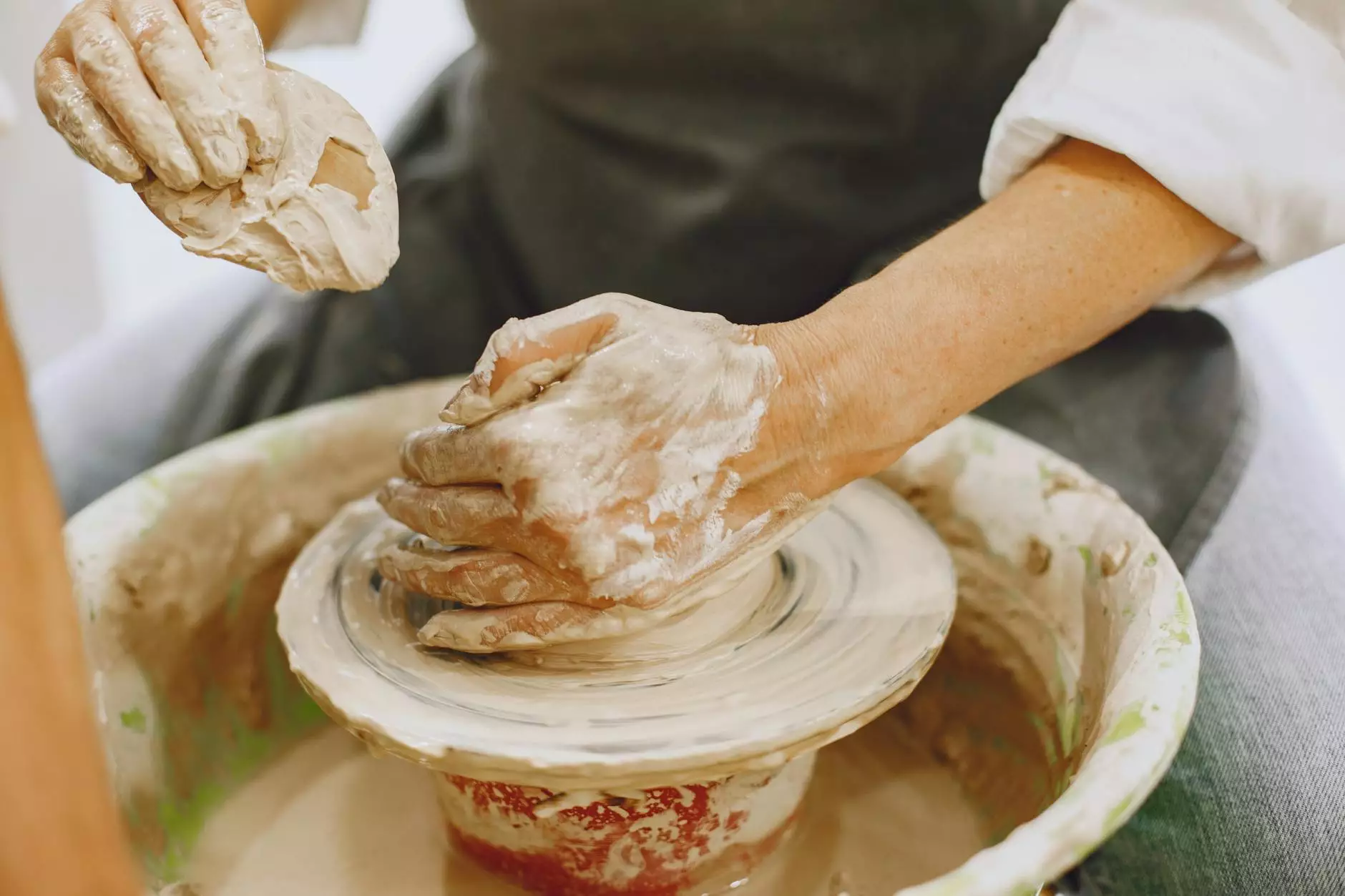
The manufacturing industry continually evolves, driven by technological advancements and changing market demands. One sector that stands out is the realm of plastic injection molding manufacturers. This process plays a vital role in producing a vast array of products that we use daily. Understanding the operations, trends, and significance of this sector can prove invaluable for business stakeholders.
What is Plastic Injection Molding?
Plastic injection molding is a manufacturing process used to produce plastic parts by injecting melted plastic into a mold. This technique is favored in various industries due to its efficiency, precision, and ability to produce high volumes of parts with complex geometries.
The Process Explained
The process of plastic injection molding can be broken down into several key steps:
- Material Selection: The manufacturing journey begins with selecting the appropriate type of plastic, which can vary based on the desired properties of the final product.
- Creating the Mold: A mold is designed and manufactured, usually from metal, to form the specific shape of the desired product.
- Heating and Injection: The chosen plastic is heated until it becomes molten and is then injected into the mold under high pressure.
- Cooling: The injected plastic cools and solidifies within the mold, taking on its final form.
- Extraction: Once cooled, the newly formed part is extracted from the mold.
Why Choose Plastic Injection Molding?
Companies are increasingly opting for plastic injection molding due to numerous benefits that elevate their products and operations:
- Efficiency: This process is incredibly efficient, allowing for mass production of high-quality parts in a relatively short period.
- Cost-Effectiveness: While the initial set-up costs can be high, the long-term savings through volume production are significant.
- Design Flexibility: Molding allows for intricate designs and has few limitations in terms of shapes and sizes.
- Minimized Waste: The process is designed to be efficient, generating minimal waste and maximizing the use of raw materials.
Market Trends in Plastic Injection Molding
To stay competitive, plastic injection molding manufacturers must adapt to ongoing market trends:
Sustainability in Manufacturing
With increasing awareness about environmental issues, sustainable manufacturing practices are critical. Manufacturers are adopting biodegradable materials and recycling practices to meet consumer demand for eco-friendly products.
Technological Innovations
The integration of advanced technologies such as automation, robotics, and artificial intelligence is revolutionizing the industry. These technologies enhance precision, improve production speeds, and reduce labor costs.
Customization and Personalization
Consumers are increasingly favoring customized products. Plastic injection molding manufacturers must pivot to accommodate personalized requests, offering tailored solutions that meet specific client needs.
Challenges Faced by Plastic Injection Molding Manufacturers
Despite the numerous advantages, the industry also faces several challenges:
- Rising Material Costs: Fluctuating prices of raw materials can affect profitability and pricing structures.
- Skilled Labor Shortage: The industry struggles to find skilled workers who are experienced with advanced molding techniques and machinery.
- Maintaining Quality: As demand increases, manufacturers must ensure consistency in quality while scaling production.
The Future of Plastic Injection Molding
The future of the plastic injection molding industry looks promising, characterized by significant opportunities and trends:
Growth in Emerging Markets
Global demand for plastic products is rising, particularly in emerging markets. Manufacturers that strategically position themselves in these regions can capitalize on this growth.
Increased Automation
The rise of Industry 4.0 is transforming manufacturing processes. Manufacturers that embrace automation and smart manufacturing can enhance operational efficiency and effectiveness.
Strategic Partnerships and Collaborations
Building alliances with suppliers and technology providers can enhance innovation and responsiveness to market changes. Collaboration is key to staying ahead in a competitive landscape.
How to Choose a Plastic Injection Molding Manufacturer
When selecting a business partner, consider the following criteria:
- Experience: Look for manufacturers with a proven track record in plastic injection molding.
- Certification: Ensure that the company adheres to industry standards and has necessary certifications.
- Technology: Evaluate the technology utilized in the manufacturing process and how it aligns with your needs.
- Customer Support: Strong customer service can make a significant difference in overcoming business challenges.
Conclusion
In summary, the world of plastic injection molding manufacturers presents vast opportunities and challenges. Businesses within this sector must stay informed about current trends, invest in technology, and prioritize sustainability to ensure their continued success. Understanding the intricacies of this manufacturing process is essential for any company looking to thrive in an increasingly competitive market. By recognizing and addressing these factors, manufacturers can position themselves favorably for the future, contributing to a more innovative and sustainable manufacturing landscape.
For businesses looking to navigate the complexities of plastic injection molding, partnering with a skilled and experienced manufacturer is key to achieving operational excellence and delivering exceptional products to the marketplace.