The Art and Science of Plastic Mold Fabrication
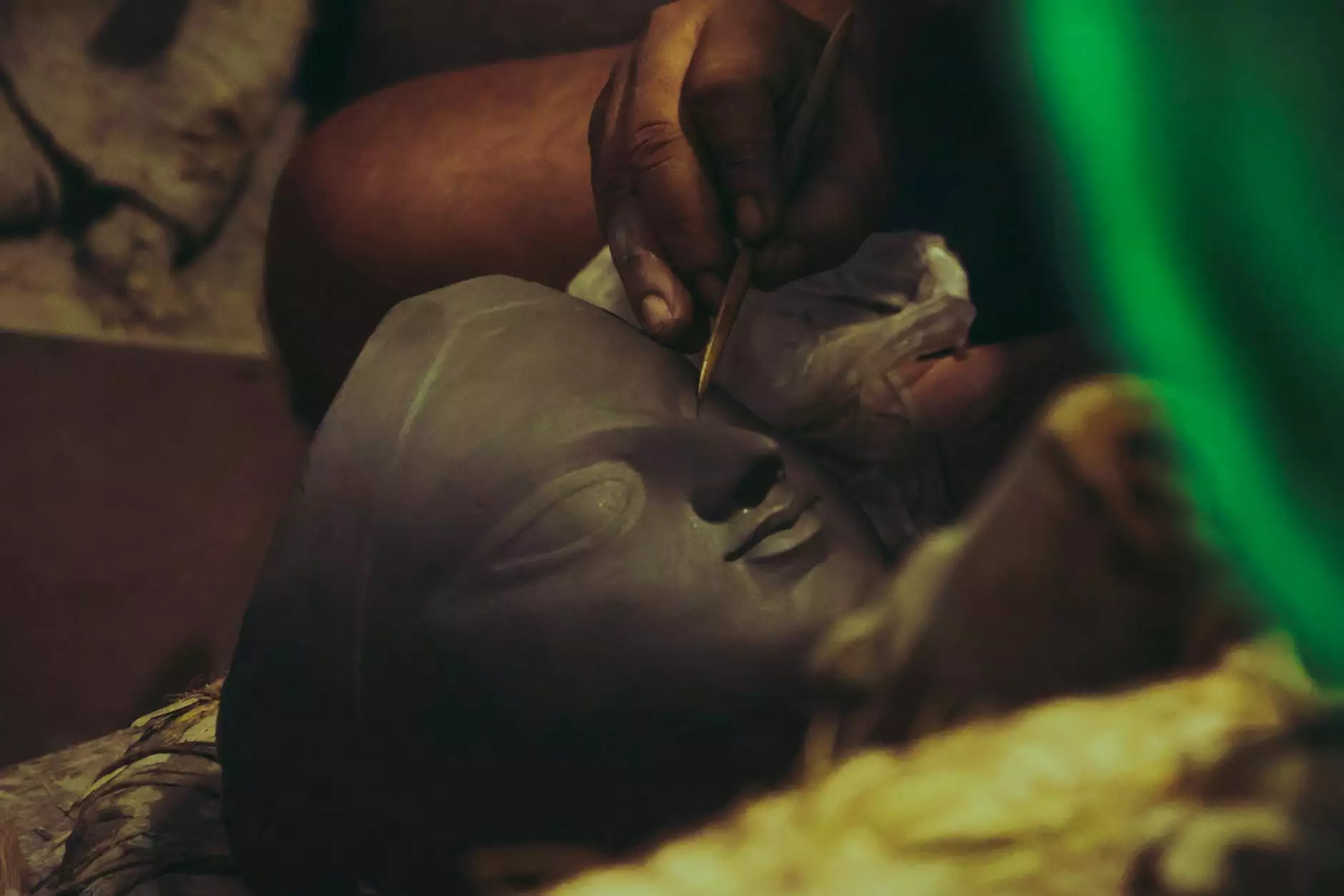
In today's fast-paced manufacturing landscape, plastic mold fabrication has emerged as a cornerstone of innovation and efficiency. With the rapid growth of industries relying on plastic products, understanding the intricate processes involved in mold fabrication is crucial for businesses aiming to stay ahead in the competitive market. This guide delves into the various aspects of plastic mold fabrication, showcasing its significance, methodologies, and the exceptional contributions of Hanking Mould as a renowned plastic injection mould manufacturer.
Understanding Plastic Mold Fabrication
Plastic mold fabrication refers to the comprehensive process of designing and creating molds used for producing plastic parts. This intricate procedure encompasses several stages, from initial conception and design to the final production of high-precision molds. The importance of mold fabrication cannot be overstated, as it lays the foundation for product efficiency, cost-effectiveness, and quality consistency.
The Significance of Plastic Mold Fabrication
As industries evolve, the demand for sophisticated plastic components grows. Plastic mold fabrication plays a vital role in multiple sectors, including automotive, consumer electronics, medical devices, and consumer goods. By leveraging advanced mold-making techniques, businesses can achieve:
- Cost Savings: Efficient molding processes reduce material waste and labor costs.
- Design Flexibility: Modern molds can be designed for complex geometries and intricate details.
- Scalability: Molds can be replicated for mass production, ensuring consistency across thousands of units.
- Enhanced Product Quality: High-precision molds contribute to superior finish and dimensional accuracy.
The Mold Fabrication Process
The journey of plastic mold fabrication begins with a well-thought-out design, which entails several steps:
1. Design and Prototyping
Every successful mold starts with an innovative idea. Designers utilize CAD (Computer-Aided Design) software to create 3D models of the intended product and mold. This digital prototype allows for adjustments before physical creation, ensuring that the final product meets customer requirements.
2. Material Selection
The choice of materials for mold construction is critical. Common materials include steel and aluminum, with each offering unique benefits. Steel molds are generally used for high-volume production due to their durability, while aluminum molds are favored for lower production runs due to their cost-effectiveness and ease of manufacture.
3. CNC Machining
Once the design is finalized, CNC (Computer Numerical Control) machining is utilized to fabricate the mold. This process involves using precise machinery to cut and shape the mold material accurately, ensuring that all specifications are met with outstanding precision.
4. Assembly and Testing
After machining, the components of the mold are assembled and subjected to rigorous testing. This phase is crucial for identifying any issues that may affect the quality of the final product. Testing ensures that the mold operates smoothly, producing parts that adhere to stringent quality requirements.
5. Production
With a verified mold in hand, the production phase commences. The mold is placed in an injection molding machine, where plastic pellets are heated and injected into the mold cavity. After cooling, the mold is opened, and the finished product is ejected. This efficient sequence allows for large quantities of identical components to be produced swiftly.
Benefits of Plastic Mold Fabrication
The advantages of investing in plastic mold fabrication are substantial. Here are key benefits that businesses can enjoy:
- Enhanced Production Speed: Automated processes allow for rapid production, reducing the time to market.
- Consistency: Molds guarantee uniformity across all manufactured products, enhancing brand reliability.
- Waste Reduction: Precise fabrication processes minimize material waste, contributing to sustainability.
- Improved Performance: Advanced molding techniques result in stronger, more durable products.
Choosing the Right Plastic Mold Maker
Selecting the right plastic mold maker is crucial for ensuring success in your manufacturing endeavors. Key considerations include:
- Experience: Look for a company with a proven track record in mold making.
- Technological Proficiency: A company that utilizes the latest fabrication technologies will provide superior products.
- Customer Support: Ensure they offer excellent customer service, guiding you through the process from design to production.
- Quality Assurance: Opt for a manufacturer that emphasizes quality checks and compliance with industry standards.
The Role of Hanking Mould in the Industry
Hanking Mould stands out as an industry leader in plastic injection mould manufacturing. With years of expertise and a commitment to excellence, they have garnered a reputation for delivering high-quality molds tailored to diverse applications. Their use of advanced technology and a skilled team enables them to offer:
- Customization: Tailored molds designed to meet the specific needs of clients, regardless of industry.
- Cost-effective Solutions: Competitive pricing without compromising on quality.
- Timely Delivery: Efficient processes ensure that projects are completed on schedule.
- After-sales Support: Ongoing support for maintenance and adjustments post-production.
Future Trends in Plastic Mold Fabrication
As the industry continues to evolve, several trends are shaping the future of plastic mold fabrication:
1. Increased Automation
Automation is gradually taking over various stages of the mold-making process. CNC machines and robotic arms are enhancing production speed while minimizing human error, thereby improving overall output quality.
2. Sustainable Practices
With the world becoming increasingly eco-conscious, sustainable practices in mold fabrication are gaining importance. Techniques that reduce waste and use recyclable materials are becoming the norm.
3. Advanced Materials
Innovations in material science are leading to the development of new mold materials that can withstand higher temperatures, reduce wear and tear, and improve product performance.
4. 3D Printing Integration
3D printing technology is being integrated into the mold-making process, allowing for rapid prototyping and modifications without significant downtime. This integration is revolutionizing how molds are designed and produced.
Conclusion
In conclusion, plastic mold fabrication is a pivotal aspect of modern manufacturing that offers numerous advantages to businesses across various industries. With efficient processes and high-quality outcomes, investing in expert mold fabrication services can significantly impact your production capabilities. Hanking Mould exemplifies excellence in this area, providing high-end solutions tailored to meet the unique needs of their clients.
As industries continue to innovate, staying informed about the latest trends and technologies in plastic mold fabrication is essential for any business looking to thrive in a competitive marketplace. For unparalleled expertise and support in mold fabrication, consider partnering with Hanking Mould to unlock your production potential.