Understanding Precision Injection Molding in Metal Fabrication
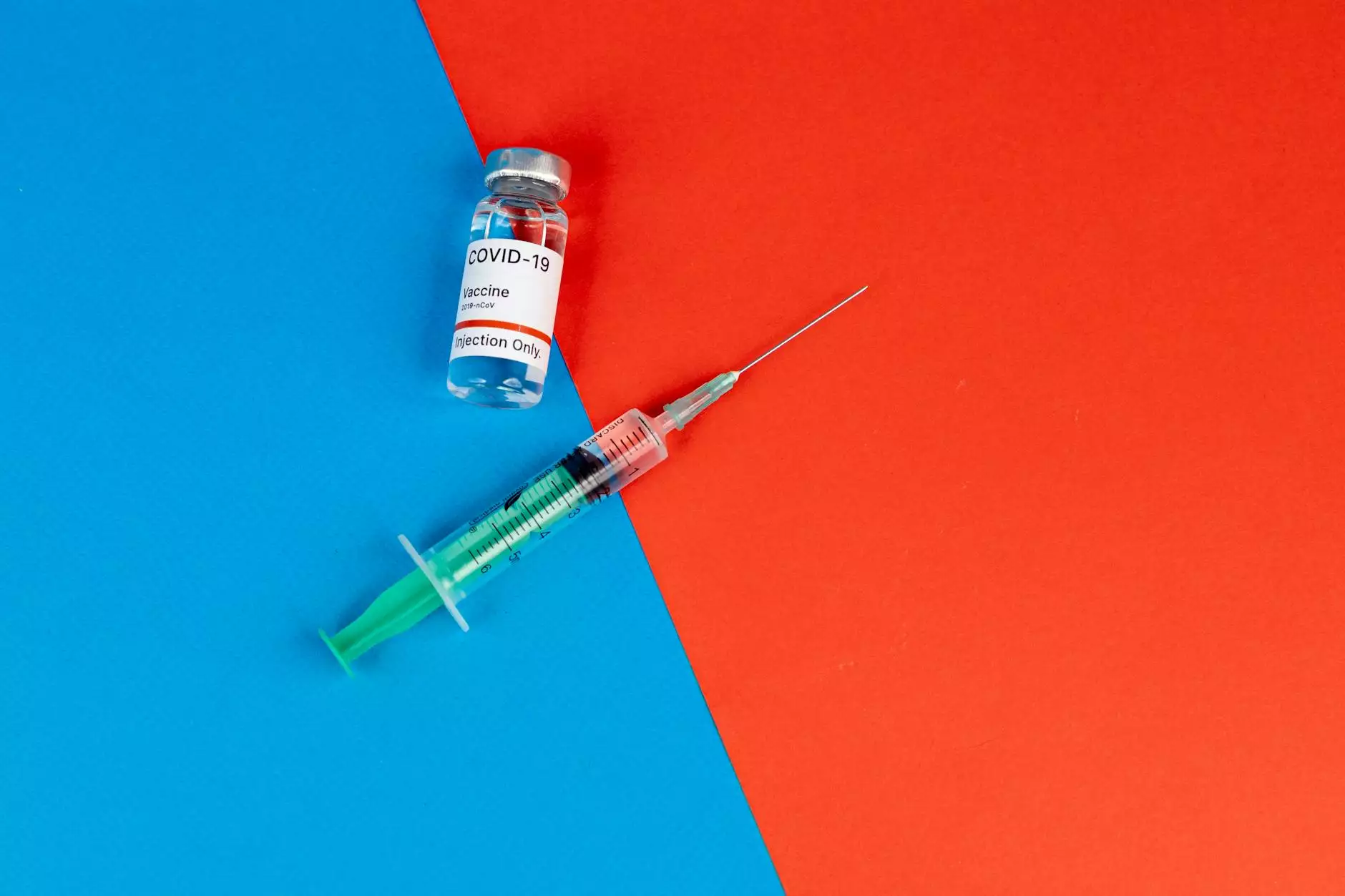
Precision injection molding is a revolutionary manufacturing process that plays an essential role in the field of metal fabrication. This method allows for the creation of intricate and highly accurate components with minimal waste, making it a preferred choice for industries seeking efficiency and quality. In this article, we will delve into the intricacies of precision injection molding, its applications in metal fabrication, and why it has become a cornerstone for businesses like deepmould.net.
What is Precision Injection Molding?
At its core, precision injection molding is a manufacturing process used to produce parts by injecting molten material into a mold. This method is particularly useful for creating detailed components that require high levels of precision and repeatability. The materials used can include various types of metals, plastics, and composite materials, depending on the specific industry requirements.
The Process of Precision Injection Molding
The process of creating a precision injection mold involves several carefully controlled steps. Here’s a comprehensive breakdown of the procedure:
- Designing the Mold: The first step is to design the mold which is typically carried out using computer-aided design (CAD) software. This step is critical, as the mold design will determine the final product's accuracy and quality.
- Creating the Mold: After finalizing the design, the mold is manufactured using advanced techniques, which can include CNC machining or 3D printing for rapid prototyping.
- Injection Process: Molten material is injected into the mold under high pressure. The precision of this step is crucial, as any variations can lead to defects in the final product.
- Cooling Phase: Once the material is injected, it needs to cool and solidify within the mold. Proper cooling is essential for ensuring the dimensional accuracy of the component.
- Mold Release: After cooling, the mold is opened, and the finished part is ejected. Additional finishing processes may be applied, such as trimming or polishing.
Benefits of Precision Injection Molding
Choosing precision injection molding offers various advantages that contribute to operational excellence and competitive edge in manufacturing. Here are some of the key benefits:
- High Precision: The advanced technology used in precision injection molding ensures that products have tight tolerances, making them suitable for high-performance applications.
- Minimized Waste: The process is designed to utilize materials efficiently, significantly reducing scrap and waste during manufacturing.
- Cost-Effectiveness: While the initial investment for designing and creating a mold can be high, the long-term production efficiency and material savings make it a cost-effective solution.
- Versatility: Precision injection molding supports a wide range of materials and can be used to create various components for different industries, including automotive, aerospace, and consumer goods.
- Scalability: Once a mold is created, it can produce thousands of identical parts quickly, making it ideal for businesses that require high-volume production.
Applications of Precision Injection Molding in Metal Fabrication
The applications of precision injection molding extend across multiple sectors within metal fabrication. Here are some noteworthy applications:
Automotive Industry
In the automotive industry, precision parts made from injection molds are crucial. Components such as engine blocks, gears, and housings benefit from the reliability and precision delivered by this process.
Aerospace Sector
In aerospace, safety and accuracy are paramount. Injection molded parts are often used in aircraft bodies, engine components, and electronic housings, where precision is non-negotiable.
Consumer Electronics
The consumer electronics market demands high-quality parts for devices like smartphones and laptops. Precision injection molds ensure that components such as casings, connectors, and circuit boards are produced with the utmost accuracy.
Medical Devices
Medical technology often requires components to be manufactured with exceptional precision. Products such as surgical instruments and diagnostic devices greatly benefit from the capabilities of precision injection molding.
Challenges in Precision Injection Molding
Despite its advantages, businesses must also navigate several challenges associated with precision injection molding:
- High Initial Costs: The upfront investment in mold design and manufacturing can be substantial, which may deter some smaller businesses.
- Complexity of Mold Design: Designing a mold that meets the precision requirements can be complex and labor-intensive, demanding advanced skills and expertise.
- Material Selection: The choice of materials is critical. Not all metals and plastics are suited for the injection molding process, thus proper material selection is vital to achieving desired results.
Conclusion: The Future of Precision Injection Molding
The landscape of precision injection molding is ever-evolving with technological advancements. As industries continue to pursue greater efficiency and precision, the adoption of newer techniques such as automated processes, advanced CAD software, and AI-driven quality control will become more common. Companies like deepmould.net will be at the forefront of this transformation, leading the charge in delivering high-quality, precision-engineered products.
Ultimately, the benefits of precision injection molding, from cost savings to improved product quality, firmly establish it as a vital component of modern manufacturing. As businesses strive for excellence, understanding and investing in precision injection molding will be key to staying competitive in the global market.